Dixon rings were developed in 1946 by Dr Olaf George Dixon while working for ICI and are currently used where high performance is essential. There are a number of published papers on the characterisation of Dixon rings as used in distillation applications; however, there is little published work on the counter current (scrubbing) performance of Dixon rings. Croft Engineering Services have developed a revolutionary manufacturing method for Dixon rings that can be used in both counter current absorption (scrubbing columns) including scrubbing of CO2 from air, as well as hard distillation separations such as tritium from water. This cylindrical mesh item of small size in comparison to the market leaders (Pall rings, Intalox saddles) offers superior performance in a range of applications.
About Dixon Rings
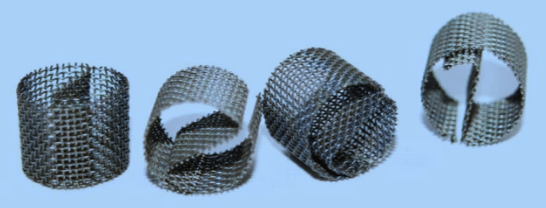
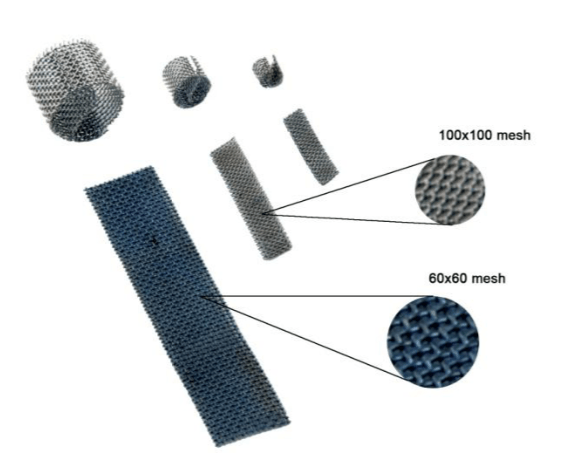
Packed columns utilising filter media for chemical exchange are amongst the most common devices used in the chemical industry for reactant contact optimisation. Dixon rings, manufactured from Stainless Steel woven wire mesh with a cross member, offer significant performance advantages to alternative random column packings, particularly where space is critical and so small diameter high efficiency columns are vital. The performance of Dixon rings is comparable to that of structured packing which is extremely column specific, and carries large installation and other costs. Dixon rings comparable performance comes with the ease of “dumping” the packing in, which reduces the initial installation cost as well as offering cost savings when cleaning or replacement is required. Dixon rings can also be used in retrofits where the performance of the current packing is not delivering the performance required.
Dixon rings can be used in counter current absorption applications, including waste gas scrubbing, acid gas removal, and carbon capture. They can also be used for distillation applications and are specifically used for what can be classed as “difficult” separations where the boiling points of the constituent parts are very close such as in tritium/water separation at 101.4oC/100.0oC respectively.
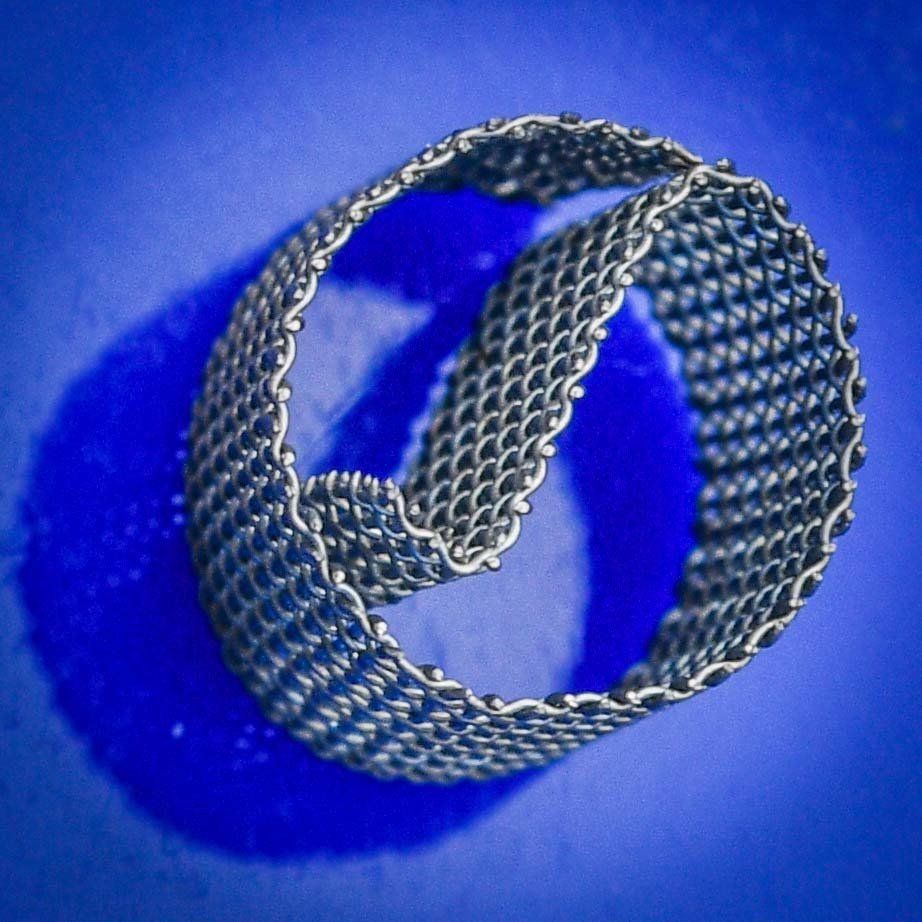
Dixon rings are formed from flat sections of 100x100 mesh or 60 x 60 mesh. The mesh is then wound to form a cylindrical shape with the cross bar to both provide rigidity to the ring, to avoid crushing and to provide extra surface area. Woven wire mesh is used in a multitude of filtration applications to remove physical particulates from a liquid
stream, however here the woven wire mesh is being utilised for the generation of a liquid film which provides a chemical separation without the requirement for additional energy to promote the separation. Rather, the process of separation (or transfer) occurs through ‘intimate’ contact between liquid and gas.
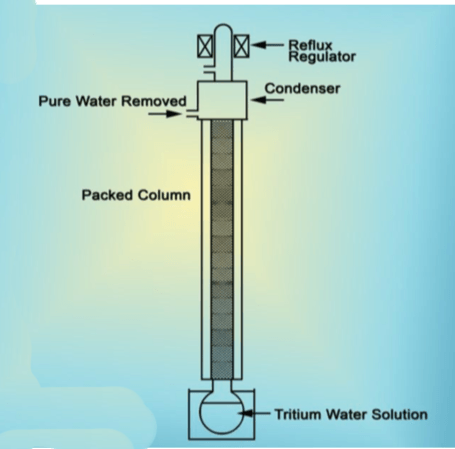
PACKED COLUMNS
Packed columns are used within a range of industries to allow intimate contact between two immiscible/partly immiscible fluids which can be liquid/liquid or liquid/gas. The fluids are usually passed in counter current flow through the column with the gas or liquid entering at the base of the column and a liquid entering from the top. The example studied in this paper is that of a liquid/gas absorption process where soluble carbon dioxide is passed into the base of the column and water passes into the top of the column, the soluble gases being scrubbed by means of the water. Packed columns can also be used for distillation where the more volatile components of a mixture, (in simplest form, binary mixture) undergo transformation due to input of heat into the vapour phase. The less volatile compound will condense out into the liquid phase and can be removed, providing an efficient means of separation. Packed columns as mentioned above can also be used for liquid/liquid extractions where the solute is transferred between solvents.
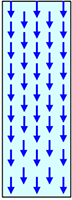
Flow
To obtain an effective mass transfer within a single column it is essential that a packing is selected which will support a large surface area for mass transfer between the two
phases. It is also essential that the flow is not just laminar flow through the column; the packing must promote the formation of a turbulent flow. Time and resources must be put into selection of the most appropriate packing for the application that produces turbulent flow and sufficient surface area
The actual column itself can be constructed from a range of materials depending on the application; materials include ceramic, glass, metals and plastics. The column is mounted vertically causing a water flow as shown above. This prevents the liquid all flowing to one side resulting in ineffective use of some areas of the column.
The packing within the column rests on packing supports which has the greatest free area possible to promote constant flow out of the column with minimal resistance. The simplest support is a grid consisting of bars evenly spaced slightly smaller than the slimmest unit of packing. The gas inlet is designed so that the liquid flowing out of the column and the gas are not competing which would promote unstable operation as the gas bubbles through in bursts, against the water, instead the gas inlet is positioned above the level of the liquid drain. At the top of the column a liquid distributor is installed to promote homogeneous separation of the liquid over the whole packed bed. A similar arrangement may be required within the packed bed to redistribute the flow. The gas inlet is also designed to promote the uniform distribution across the cross section of the column.
Column diameters vary from 25mm for small laboratory columns up to 4.5metres for large industrial columns which can also be up to 30metres tall. The pressure within these columns varies from vacuum to extremely high pressure.

TYPES OF PACKINGS
Packings can be divided into three main classes: Broken solids which are the cheapest type of packing available in sizes of about 10mm-100mm; Shaped packing including the Raschig rings and Pall rings, which are used due to their high performance characteristics and low pressure drop; and structured (grid packing). Although broken solids offer good corrosion resistance they do not offer the same liquid flow or effective surface area that is offered by shaped packings. Packings should be of uniform size to produce a bed of standard characteristics with the desired performance.
The size of packing used determines the column size parameters, performance and more noticeable initially, the cost. Generally as the size of the packing increases the cost and pressure drop decrease. However, this tends to be accompanied by a decrease in mass transfer coefficient, leading to a decrease in performance, so to obtain the required overall column performance, large towers are required. Thus an increase in packing size does not always result in a decrease in overall cost.
Normally column diameters should be at least 8 times that of the packing size. In columns of smaller diameter liquid distribution is poor leading to a decrease in performance.
Structured packings which are relatively easy to manufacture are usually used in sections in columns. They can be fabricated from a number of materials and because of relatively large gaps between the grids, they give low pressure drops, this large open area also allows structured packing to accept liquid with suspended solids. However structured packing tends to promote laminar flow where the liquid flows at high flow rates from grid to grid without being broken up into droplets, the later of which is of course desired for efficient separations.
For applications where high performance is essential (usually laboratory purposes) column packings such as the Dixon ring, Lessing ring, and knitted mesh (a fine wire mesh) have been developed. These packings are superior
to larger packings, in that they offer a very large surface area, which once pre wetted, is all available for mass transfer to occur. These packings have been used in columns up to 500mm in diameter.
5. THEORY OF APPLICATION
Carbon dioxide is a greenhouse gas and a major contributor at that. Carbon dioxide is a by-product in the burning of fossil fuels and an effective method of scrubbing this carbon dioxide to prevent it escaping to the atmosphere is often an essential requirement. Investigation of packing performance in counter current mass transfer applications using carbon dioxide and water is therefore relevant and topical.

DESIGN AND OPERATING REQUIREMENTS Design requirements
To maximise the efficiency of a column packed with Dixon rings the diameter must be a minimum of six times that of a singular unit Therefore when working with the 1/8”(3.175mm) Dixon rings the column must be a minimum of 20mm however it is advisable to design columns with greater diameter than this.
The column must also have an easy access both top and bottom for filling and emptying the column of Dixon rings although this will be an infrequent requirement.
6.2 Operating requirements
The principle behind the counter current application of Dixon rings is the formation of a liquid film over the rings, in which the gas passing up over this film is “scrubbed”. One specific requirement of Dixon rings then is the need for pre wetting. If operation is started without pre wetting the rings, efficiency is greatly reduced. Pre wetting is achieved by flooding the column slowly (i.e. over a period of at least an hour) the bottom valve is shut and the liquid allowed to run in and “flood the column” at a low flow which both stops air locks and allows all the Dixon rings to be thoroughly wetted. It is advisable to leave the column flooded between uses.
Once the column is fully flooded the valve at the base of the column is opened slowly and the desired liquid flow selected, the column is then left for a further hour to reach equilibrium before any gases, clean or dirty are shown to the column.
7. CHARACTERISATION OF PACKING PERFORMANCE 7.1 Surface area
The surface area of Dixon rings was obtained through BET surface area analysis using Krypton. Although the surface area of Dixon rings is large in comparison to other packing materials, it was still on the lower end of the operating range of typical BET surface area measurement equipment. The surface area of a 1/8” ring was quantified as 2378m2/m3, almost triple that of the common 10mm Pall ring.
7.2 Pressure drop
The pressure drop is known to be very low for Dixon rings, this allows Dixon rings to be used in reduced pressure applications as well as allowing energy savings in terms of energy consumption of pumps and blowers. The pressure drop was calculated by OG Dixon1 as mentioned above to range from 49.82-647.63pa per 305mm of packing in vapour flow rates between 30-274 mm/second. In our apparatus described here, the pressure drop was considered to be negligibly small.
7.3 Mass transfer coefficient
The Height equivalent to a theoretical plate was reported By Dixon1 to be as high as 200 plates in a 914mm length 258.mm diameter column, (a height equivalent to theoretical plate of 4.57mm). The mass transfer coefficient within this work was determined to be in the region of 463.22 mg/l/min
7.4 Liquid holdup
The quantification of both dynamic and static liquid holdup is required. The dynamic liquid hold up is the volume of water in the column at any one point during normal operation. This quantity is very important due to its relation with wetted area, pressure drop, flooding characteristics and transient behaviour of the column. This quantity is measured by closing both the inlet and outlet flows and then collecting the liquid in the column. Most packings promote the path of water to the outer walls of the column resulting in a decrease in efficiency meaning that regular redistributor plates are required. Dixon rings however promote the funnelling of liquid into the centre of the column causing a visual effect of a very low dynamic holdup although at maximum operating flow the column is approximately 80% full. Dixon (1948)1 in his work measured the dynamic liquid holdup to be between 10-48 grams per 645mm2 of the column.
Most previous research, including “(Gilath, 19692, King, 19583; Leva, 19534; Norman, 19615; Shulman et al., 19556) found that for a given packing, the liquid holdup is
proportional to the liquid mass flow rate to a power of between 0.5 and 0.7. It is known (Norman, 1961)6 that the thickness of a film of liquid flowing down a plate is proportional to the cube root of the liquid flow rate. When the packing has undergone pre wetting, the wetted areas and the static holdup should reach a constant value. Change in the liquid flow rate should then affect only the dynamic holdup as a result of change in the film thickness. The difference between the experimentally found power of 0.5 to 0.7 and the theoretical one of 0.33 is attributed by Norman (1961)6 to changes in the wetted areas of the packing.2
Static liquid holdup is the volume of liquid that remains in the column after the column has drained. This is the liquid that is still forming a film over the Dixon rings. The measurement of static liquid holdup is performed by draining the column as usual, however once the liquid flow has stopped (or become very slow i.e. dripping) the drain valve is shut and the column is left for 24 hours and during this period the water runs down the column. As with dynamic liquid holdup the liquid is then drained off providing a value for static liquid holdup.
Within this research the dynamic liquid hold up was determined to be 0.71932 millimetres cubed / cubed millimetre of column and the static liquid holdup was determined to be 0.17325 millimetres cubed / cubed millimetre of column.